Nexceris used our materials science expertise to help a developer of world-class battery materials to re-engineer a lab process for added economics and safety. In preparation for working with this partner, we used utilized our proven collaboration process – LEVER – to learn about their process requirements before setting foot in a lab. This allowed the team to identify in-house technologies to reduce the cost and enhance the safety of powder processing. The LEVER process utilizes our partners’ technology and Nexceris’ expertise to allow for faster advancement to commercialization.
The Situation:
Nexceris worked with Navitas Systems, a leader in next-generation lithium ion energy storage systems, who developed world-class battery materials based on micro-porous silicon powder. The material has excellent performance in lab-scale production, but process scale-up required a re-engineering for process economics and safety. In a collaborative development effort, Nexceris scaled production from grams to kilograms while reducing per kilo costs by a factor of 25.
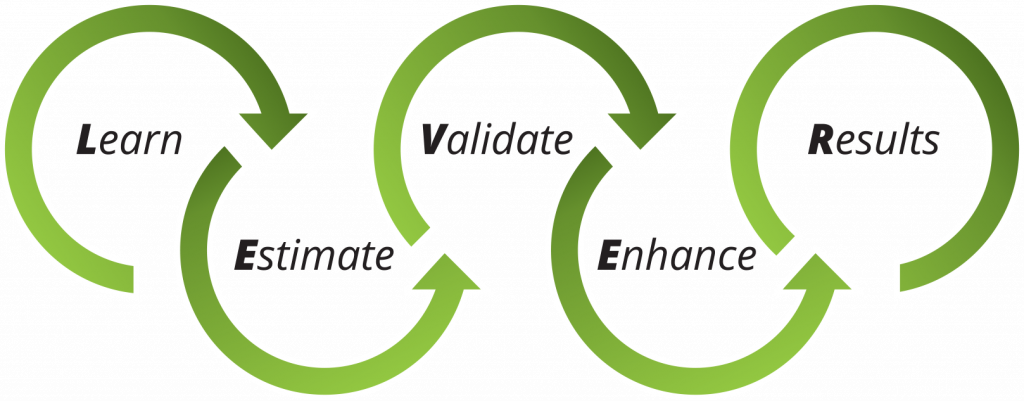
LEVER In Action:
We applied our LEVER process of: Learning, Estimating, Validating, Enhancing, and providing Results. This allowed us to scale up of the Navitas process from gram to kilogram batch sizes. See how we collaborated below:
(L)earn:
The team learned from Navitas their needs — discussions of the process requirements (end powder yield, features, economics and performance drivers) all took place before the first steps in the lab. Nexceris then tackled process scale-up by a deep review of adjacent technologies and engineering studies of materials selection and process development. The team identified In-house technologies developed for processing corrosion coatings were used to cut the cost of heat treatment, while processes derived from literature review in the mining, electronics, and metals finishing industries were adopted to reduce the cost and enhance the safety of the powder processing.
(E)stimate:
Nexceris scientists estimated the Benefit using production scale models of an envisioned process that increased production scale through, semi-continuous and continuous production. We created models of labor, capital equipment and materials costs to show how product cost would drop while maintaining product quality. These estimates also showed the importance and value of addressing materials compatibility issues—at large scale, protective coatings or exotic materials can derail project economics; it was better to address these issues at the laboratory scale.
(V)alidate:
The team validated that recommended process modifications would pay off, through lab-scale tests and delivery of powder for testing at Navitas. Each process was tested to confirm the crystal structure, physical properties and performance of the resulting powder met Navitas’ specifications. The validated processes were combined to create a scaled production line at Nexceris.
(E)nhance:
To enhance the value of the work, the scaled process line was used to confirm process reproducibility and identify process control limits. In subsequent reports, the cost model was revisited to identify the best remaining opportunities for process enhancement.
(R)esults:
The experimental work by Nexceris allowed the scale-up of the Navitas process by more than an order of magnitude, from gram to kilogram batch sizes, with a defined path to larger quantities. The safety of the process was significantly enhanced and the process can be performed at modest temperatures using existing commercial process equipment, rather than specialty alloys and polymers necessary for the starting process. Together, these improvements have reduced the cost of the anode, making demonstrations economically practical.